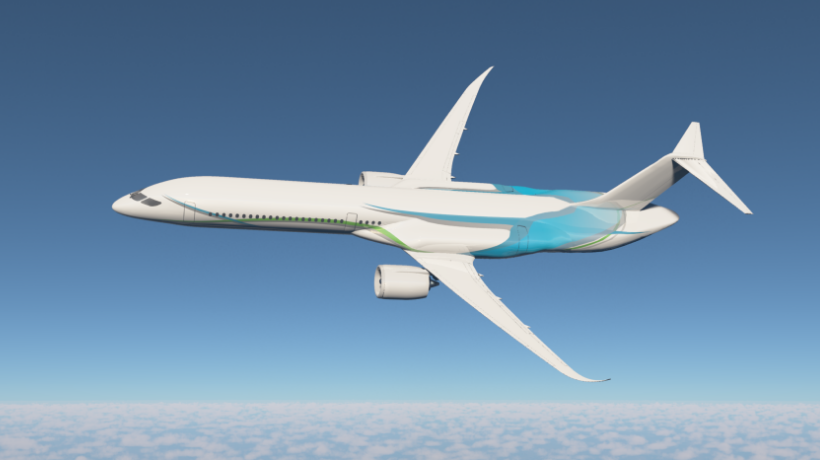
Project Overview
Although the COVID-19 pandemic has caused a global downturn in the aircraft industry, the International Air Transport Association (IATA) expects demand for air travel to recover to 2019 levels by 2023, and then, due to economic growth in emerging countries, continue sustainable annual growth levels of approximately 4%. In this context, the aircraft industry can still be considered a growth industry.
The International Civil Aviation Organization(ICAO) has adopted a goal of no increase in CO2 emissions from international aviation after 2020, and, as the demand for carbon-neutral solutions rapidly increases, is carrying out technology development related to weight reduction and efficiency improvement of aircraft bodies and engines, mainly through European and U.S. aircraft manufacturers. Furthermore, since Airbus announced its intent to launch a “carbon-neutral aircraft” in 2035 that uses hydrogen fuel and fuel cells, the competition for developing hydrogen aircraft has intensified.
The aim of this project, therefore, is to promote the development of core technologies for hydrogen aircraft, as well as technologies for dramatically lighter primary structural components with complex shapes necessary for next-generation aircraft. Through this project, the global movement toward carbon neutrality is considered an opportunity to strengthen the competitiveness of Japan’s aircraft industry. By leveraging Japan’s strengths in core technologies for hydrogen and materials, the aim of the project is also to improve Japan’s level of participation (currently about 20 to 30%) in joint international aircraft development projects.
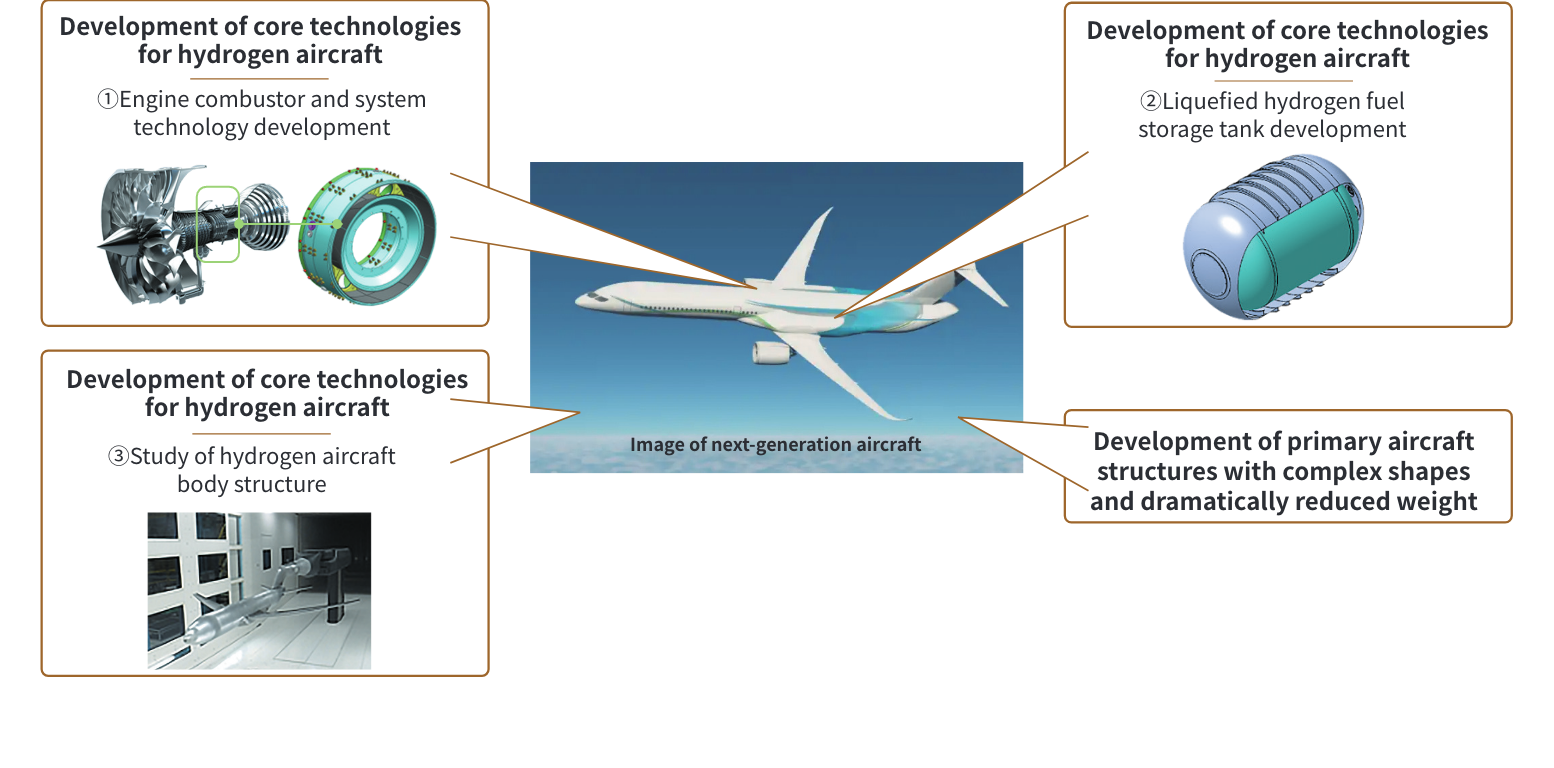
Project Features
〇 Development of core technologies for hydrogen aircraft
The aim of this project is to develop aircraft engine combustors and hydrogen fuel storage tanks suitable for hydrogen combustion with a tank weight less than twice that for stored hydrogen fuel. In addition, the structure of hydrogen aircraft will be analyzed via testing to confirm the concept of aircraft with a cruising range of 2,000 to 3,000 kilometers.
〇 Development of primary aircraft structures with complex shapes and dramatically reduced weight
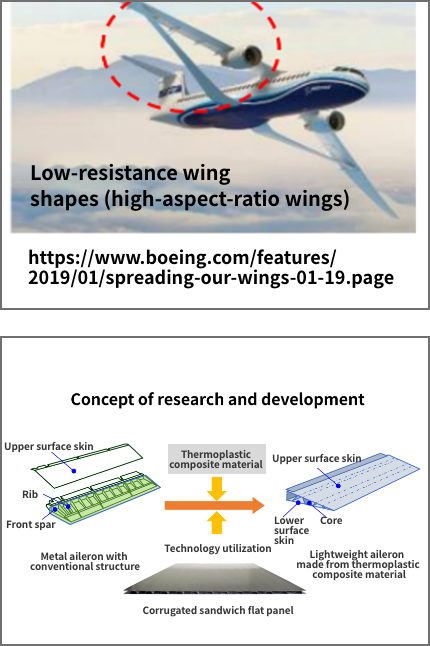
With regard to the main wings and other important structural components for small and medium-sized aircraft introduced after 2035, the aim of this project is to achieve the following: 1. Weight reduction of approximately 30% compared to existing aluminum alloy components (weight reduction of approximately 10% when compared to existing composite components), and 2. Strength improvement of 1.1 to 1.2 times the design distortion tolerance to support complex shapes and integral molding and realize further improvements in fuel efficiency.