
Project Overview
Carbon Recycling is a key technology that effectively utilizes CO2 as a resource for realizing a carbon neutral society. As of 2019, the industrial sector accounts for 29.3% of total CO2 emissions in Japan, and the chemical industry, which accounts for 18.6% of the industrial sector, emits 60.18 million tons on an annual basis.
Most of the raw materials for plastics are derived from naphtha (crude gasoline), which is obtained from refining petroleum, and about half of the CO2 emitted by the chemical industry is due to processes like cracking naphtha to produce basic chemicals such as ethylene and propylene.
In addition, about 84% of waste plastics are recycled, but some 57% of these are used as a heat source for waste-to-energy plants, etc. (thermal recycling), and are eventually discharged as CO2. So drastic measures are therefore necessary.
The aim of this project, therefore, is to develop four carbon recycling technologies related to the manufacture of plastic raw materials: advanced technology for naphtha cracking furnaces by adopting carbon-free heat sources, technology for producing chemicals from waste plastics and rubber, technology for producing functional chemicals from CO2, and technology for producing chemicals from alcohols.
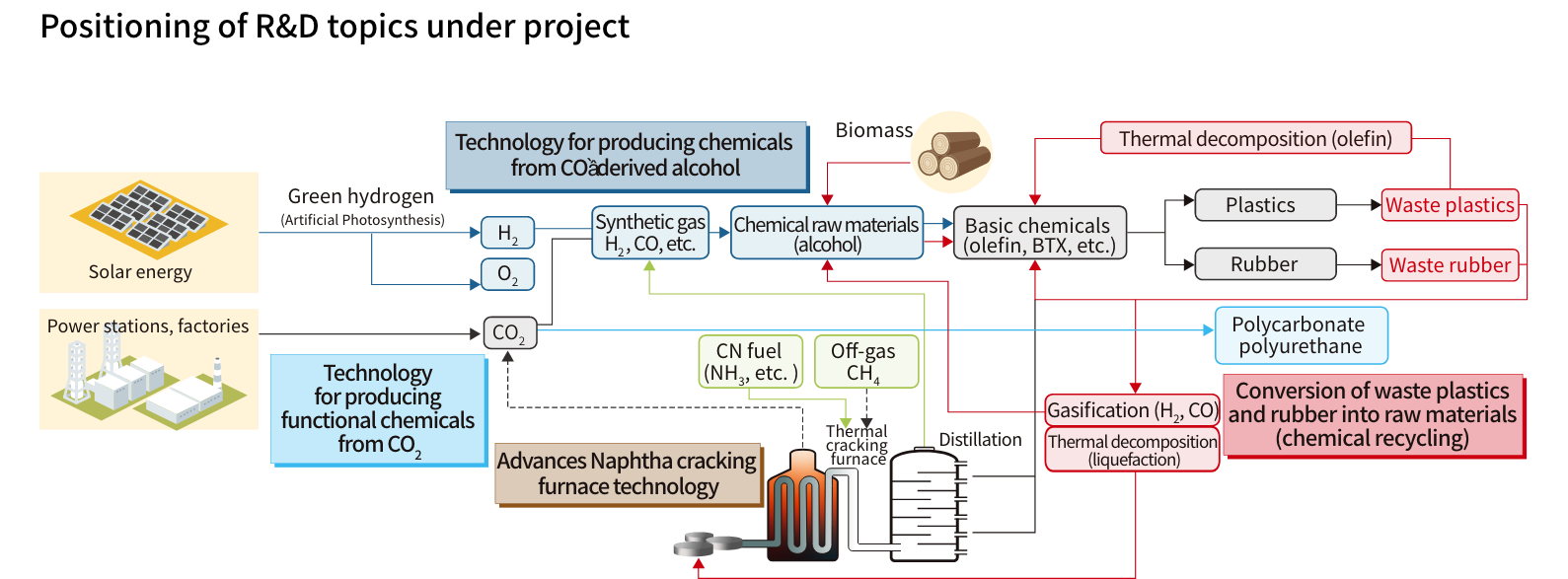
Project Features
〇 Development of advanced technology for naphtha cracking furnaces by adopting carbon-free heat sources
The aim of this project is to develop cracking furnaces and burners by 2030 that thermally decompose naphtha using ammonia and hydrogen as heat sources which emit zero CO2, and develop technologies that realize levels of energy consumption and cost during manufacturing equivalent to those of current naphtha cracking furnaces.
〇 Development of technology for producing chemicals from waste plastics and rubber
Technologies will be developed to significantly reduce CO2 emissions and manufacturing costs for gasifying, pyrolyzing, and then utilizing the biomass of waste plastics and rubber. The aim of the project is to reduce manufacturing costs 20% by 2030 compared to current recycled plastics through demonstrations at a scale ranging from thousands to tens of thousands of tons per year.
〇 Development of technology for producing functional chemicals from CO2
To realize reduced CO2 emissions and improved functionality, technologies will be developed under this project to manufacture polycarbonate and polyurethane from CO2. The aim of the project is to achieve pricing levels equivalent to ready-made products through demonstrations at a scale ranging from hundreds to thousands of tons per year by 2030.
〇 Development of technology for producing chemicals from alcohols
Photocatalysts capable of achieving high conversion efficiency (at least 10%), will be developed under this project with the aim of reducing hydrogen production costs to 30 yen/Nm³ or lower by reducing the manufacturing cost of artificial photosynthesis panels while improving their durability. The aim of the project is also to realize technologies for manufacturing high yields (80 to 90%) of basic chemicals such as ethylene and propylene from hydrogen and CO2 via alcohols and reduce CO2 emission levels during manufacturing to virtually zero.