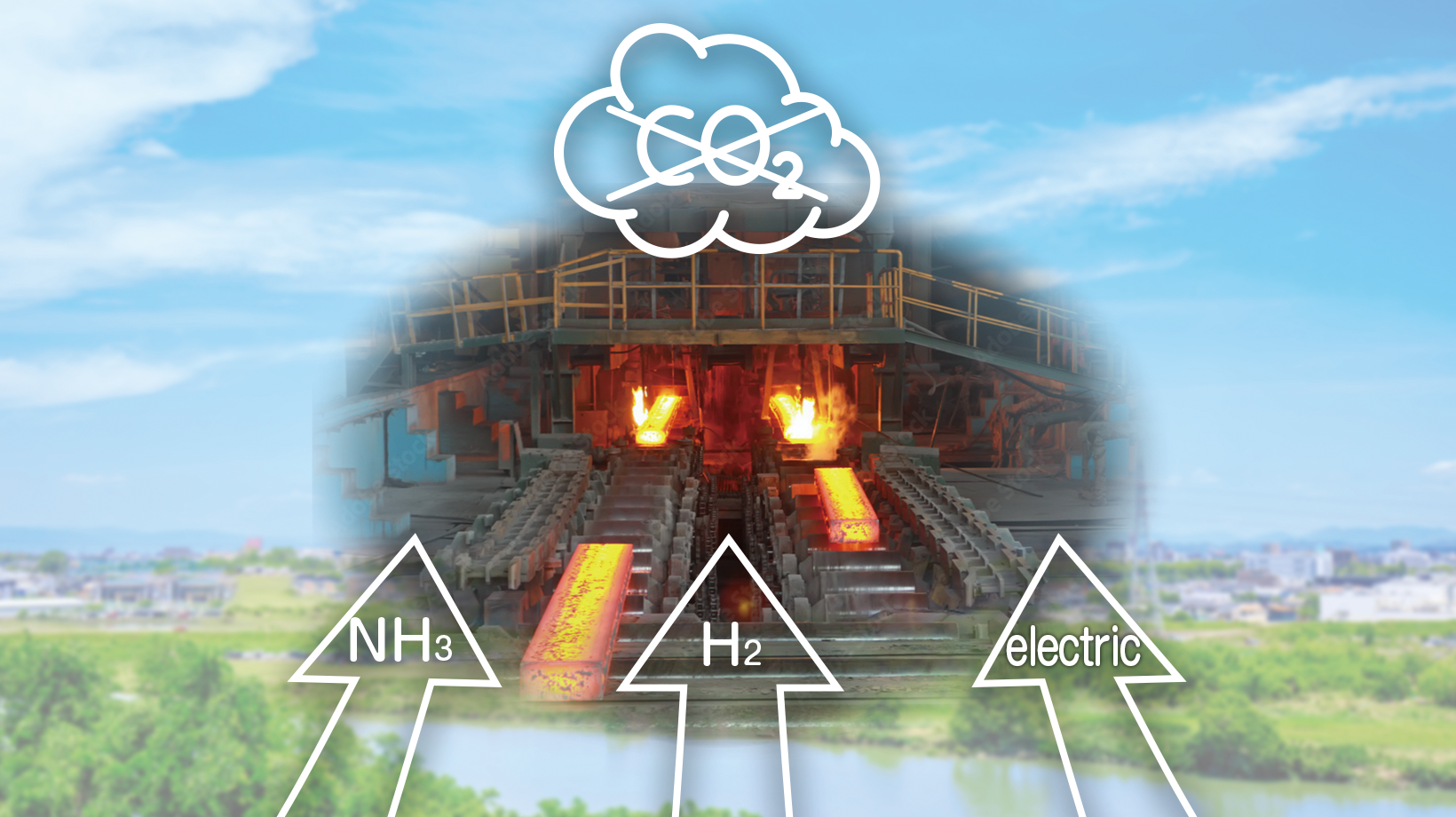
Project Overview
The production industry accounts for about 30% of the CO2 emissions of Japanese industry, and since a large amount of CO2 is emitted from industrial furnaces used in the thermal process of heating metals, the decarbonization of thermal processes in manufacturing is an urgent issue.
Industrial furnaces used for thermal processes include "combustion furnaces," which heat by burning fuel, and "electric furnaces," which heat by electricity.
Combustion furnaces are fueled by natural gas and other fossil fuels, and the use of ammonia and hydrogen, which do not emit CO2 during combustion, is promising for decarbonization, but the challenge is to establish combustion technologies that achieve combustion stability and NOx reduction, while suppressing chemical changes such as nitriding and hydrogen embrittlement in metal products.
On the other hand, electric furnaces, which do not emit CO2 when used, are a promising option for decarbonization, but there are some issues to be solved, such as the need for a special high-voltage power contract and installation of power receiving equipment when transitioning from combustion furnaces to electric furnaces.
Given the economics, efficiency, and characteristics of electric furnaces, it is important to establish a combustion furnace option as well.
This project will develop technologies for combustion furnaces compatible with ammonia and hydrogen fuels, etc., and for minimizing and increasing the efficiency of electric furnace receiving capacity, which is essential for promoting the transition from combustion to electric furnaces, with a view to establishing a supply base for zero-emission fuels in the future.
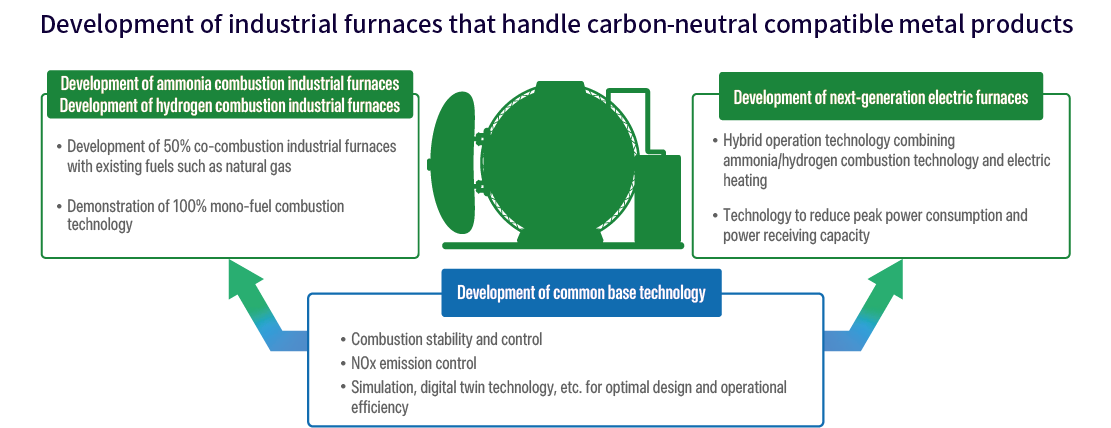
Project Features
〇 Establishment of ammonia and hydrogen combustion industrial furnace technology for handling metal products
Using ammonia or hydrogen as fuel, which does not emit CO2 when burned, the project will develop industrial furnaces and related technology that can achieve the same or better level of quality of metal products, NOx emissions, combustion stability and control accuracy, long-term operational stability, and other items compared to existing industrial furnaces.
〇 Establishment of technology to reduce the capacity of electric furnace receiving equipment and increase efficiency
The project will develop hybrid operation technology that combines ammonia/hydrogen combustion technology and electric furnaces, etc., and establish technology to reduce peak power consumption and the capacity of power receiving facilities by 30% or more.
The project will also develop technologies for utilizing waste heat from electric furnaces, increasing the output of heaters, and preventing the deterioration of resistive elements and extending the service life of resistive elements, thereby establishing energy conservation technologies that save 15% or more compared to existing electric furnaces.