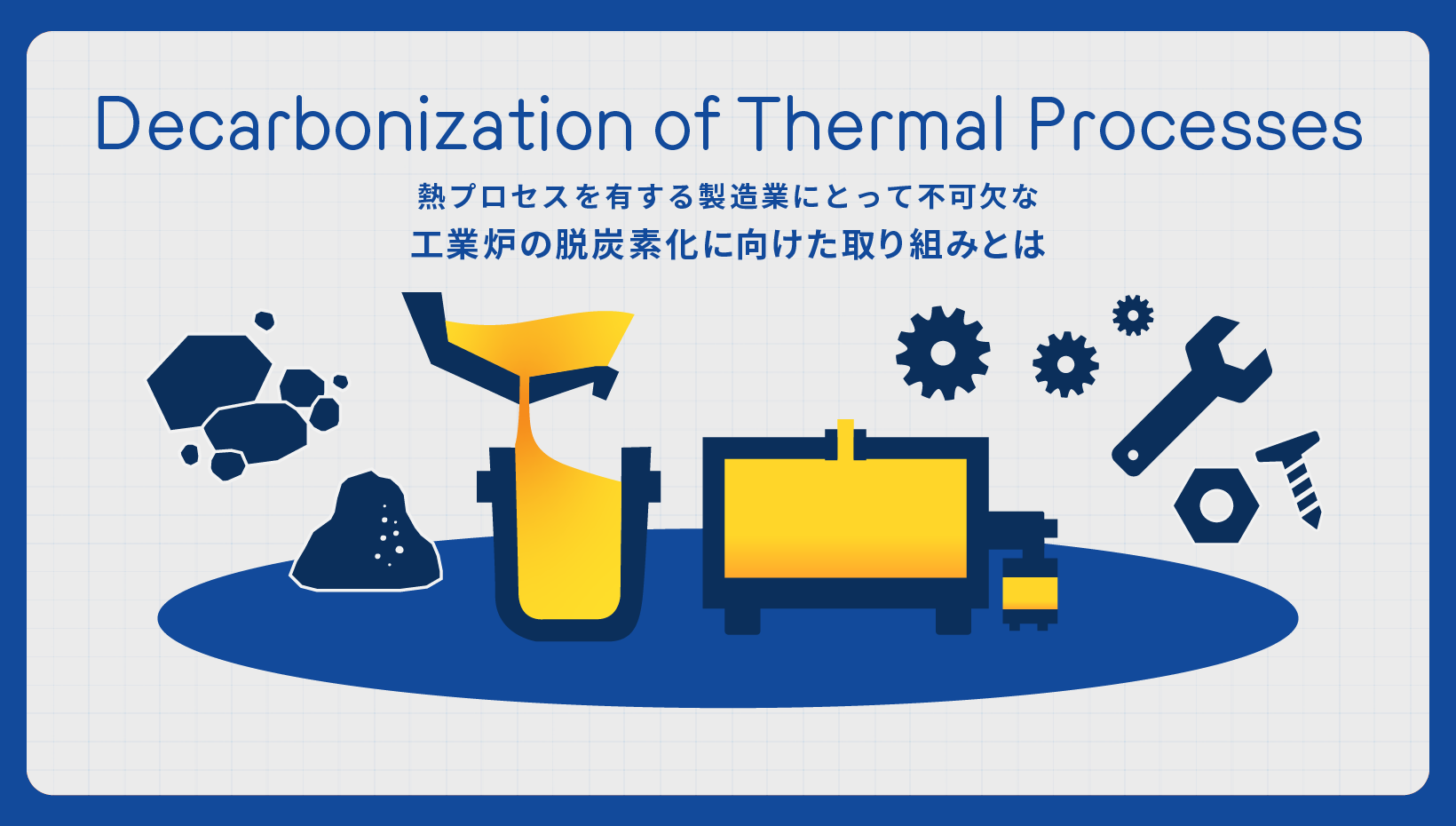
自動車
金属部品を作るのに欠かせない工業炉
製造業において金属部品は欠かせません。たとえば自動車の場合、2~3万点の部品が使われているといわれています。車が走るためのギア(歯車を組み合わせた装置)やシャフト(動力を伝動するための回転軸部品)等、必要な部品の多くは金属製です。
金属部品は、金属を加工して作ります。たとえば機械等の部品を作る際には、鉄や鋼等の原材料を溶解し、鋳型に流し込み凝固させて造形します。また、強度が求められる部品を作る際には、鋼等を加熱しハンマーやプレスで叩くことで、目的の形状に加工します。高性能、高付加価値な部品を作る際には、金属製品に加熱と冷却を組み合わせ、形を変えることなく性質を向上させます。
いずれにおいても共通するのは、金属を加工するために熱を加える、熱プロセスといわれる過程です。製造業の様々な熱プロセスで工業炉が使われています。しかし、カーボンニュートラルの達成に向けて、その工業炉を動かす際に排出されるCO2の削減が課題となってきました。
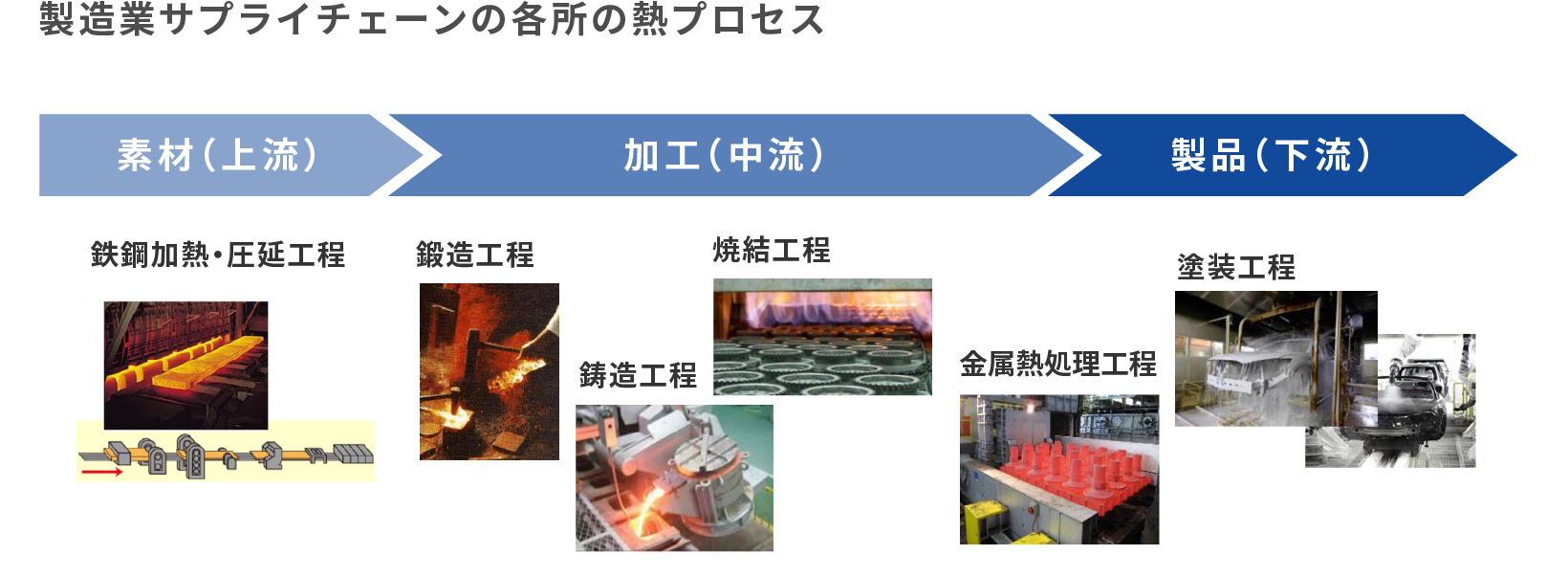
工業炉には、燃料を燃焼させて加熱する燃焼炉と、電気で加熱する電気炉があります。また、こうした熱源の違いとは別に、用途に応じた違いもあります。たとえば鉄鋼加熱炉、鍛造炉、熱処理炉、アルミ溶解炉等といった用途別の炉があり、熱源との組み合わせで仕様は多岐にわたります。
- 熱源別の主な特徴
- 燃焼炉(燃焼加熱)
・天然ガス・LPG・重油・石炭等を燃焼させた熱を利用 - 電気炉(電気加熱)
〈抵抗加熱〉
・電気抵抗による発熱を利用(例:ニクロム線ヒーター)
〈誘導加熱〉
・電磁誘導による発熱を利用(例:IHヒーター)
〈アーク加熱〉
・アーク放電(電極間で放電させるもの)の熱を利用
- 燃焼炉(燃焼加熱)
要請が高まる部品製造時のCO2排出削減
金属部品は、工業炉による熱プロセスを経て製造され、様々な産業に供給されています。特に産業構造の「川中」部分を占める金属部品関連産業においては、自動車、産業機械等の重要部品の製造にあたって、鋳造、鍛造、ダイカスト、金属熱処理、粉末冶金等、工業炉を用いた加熱プロセスが不可欠です。金属部品関連産業の国内総出荷額は16兆円、従業員は71万人にものぼります。
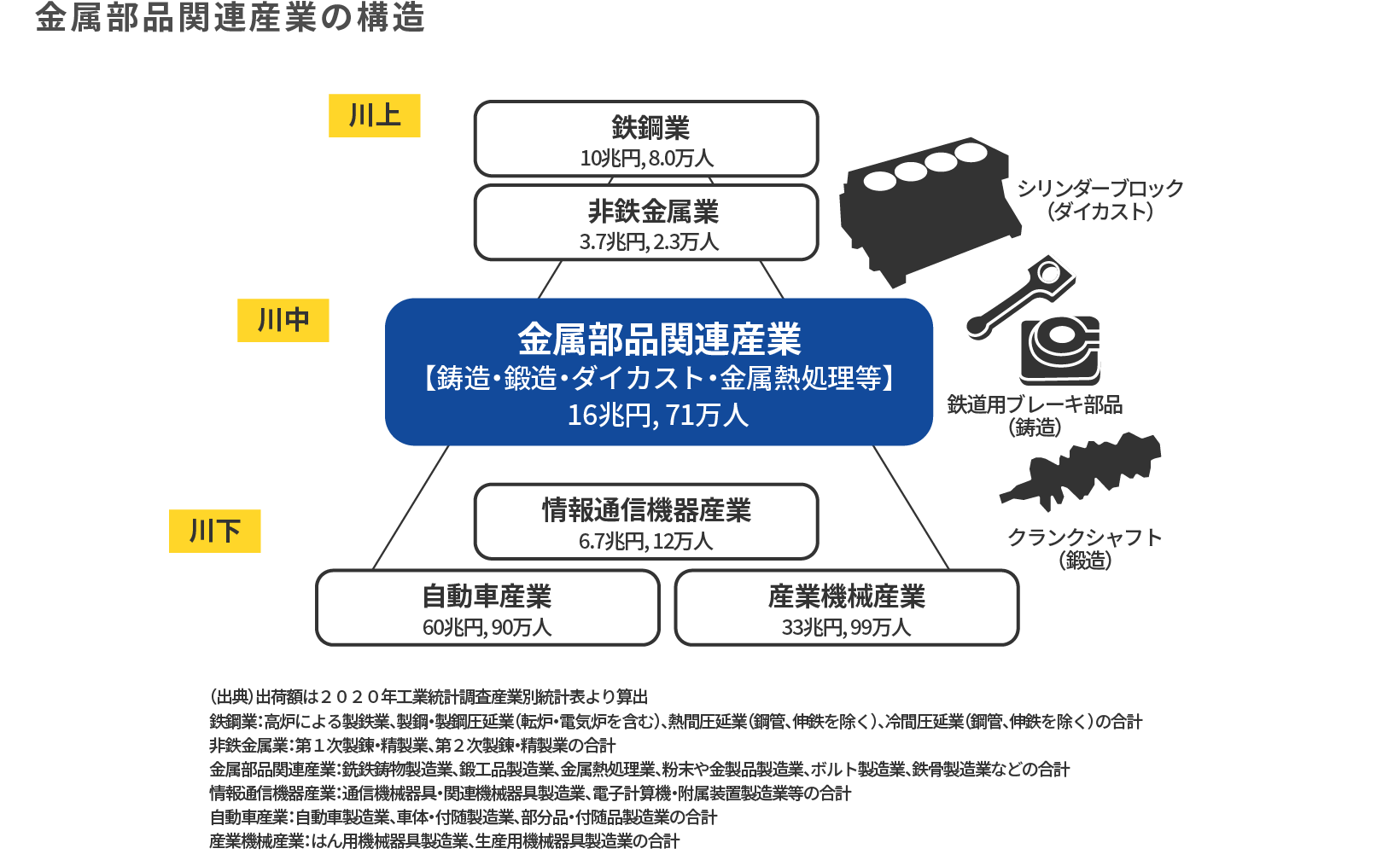
工業炉からのCO2 排出量は1.5億トンあり、我が国の排出量全体の13.5%を占めています。カーボンニュートラルを達成するためには工業炉から排出されるCO2の削減が欠かせません。
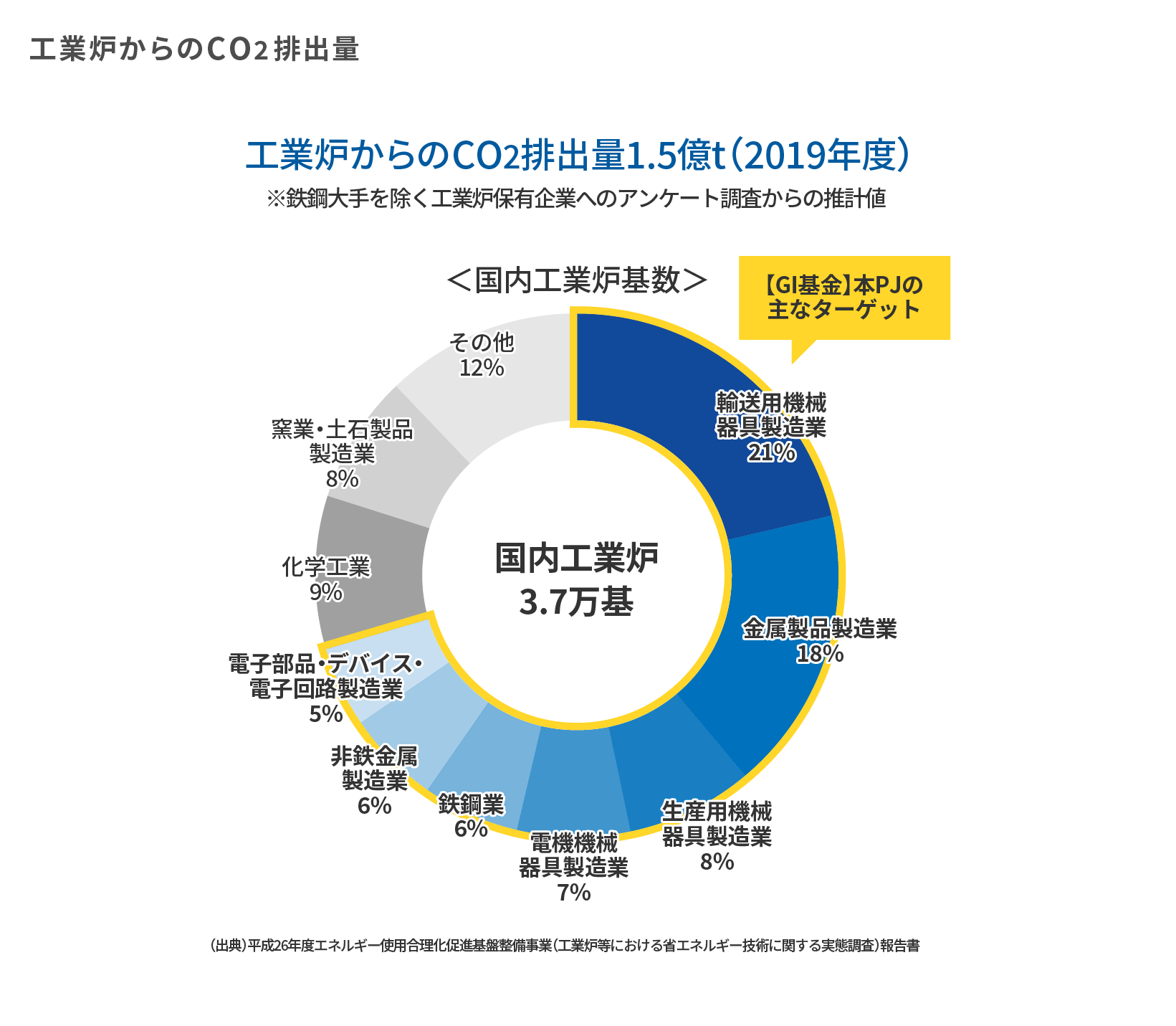
また、カーボンニュートラルの実現への要請は、各国、各産業でも進んでいます。たとえば、欧州等の自動車分野ではライフサイクルを通じた炭素排出量を評価する仕組みの導入が検討されており、金属部品関連産業等の脱炭素化を早期に実現できなければ、現状の取引関係を喪失するリスクに加え、将来的に市場参入が困難となるリスクもあります。逆に、工業炉のカーボンニュートラルが実現できれば、我が国産業の発展にも大きく寄与します。
日本の工業炉メーカーは、これまでも新たな技術を世界に先駆けて開発してきた実績があり、カーボンニュートラルを実現する新たな技術開発も期待されます。たとえば、工業炉から出る排ガスの熱によって工業炉に供給する空気を暖め、その高温空気を高速で噴射しながら燃焼を行う「リジェネレイティブバーナーシステム」は日本の工業炉メーカーが世界で初めて開発しました。従来比で30%以上の省エネを実現し、国内外で広く普及している技術になっています。
世界の工業炉需要は今後も増加していく見通しとなっており、カーボンニュートラルに対応した工業炉をいち早く実用化できれば、世界の工業炉市場に展開していくことが可能になるだけでなく、その工業炉を用いた金属部品にも新たな価値が創出されるなど、大きな経済波及効果が期待されます。
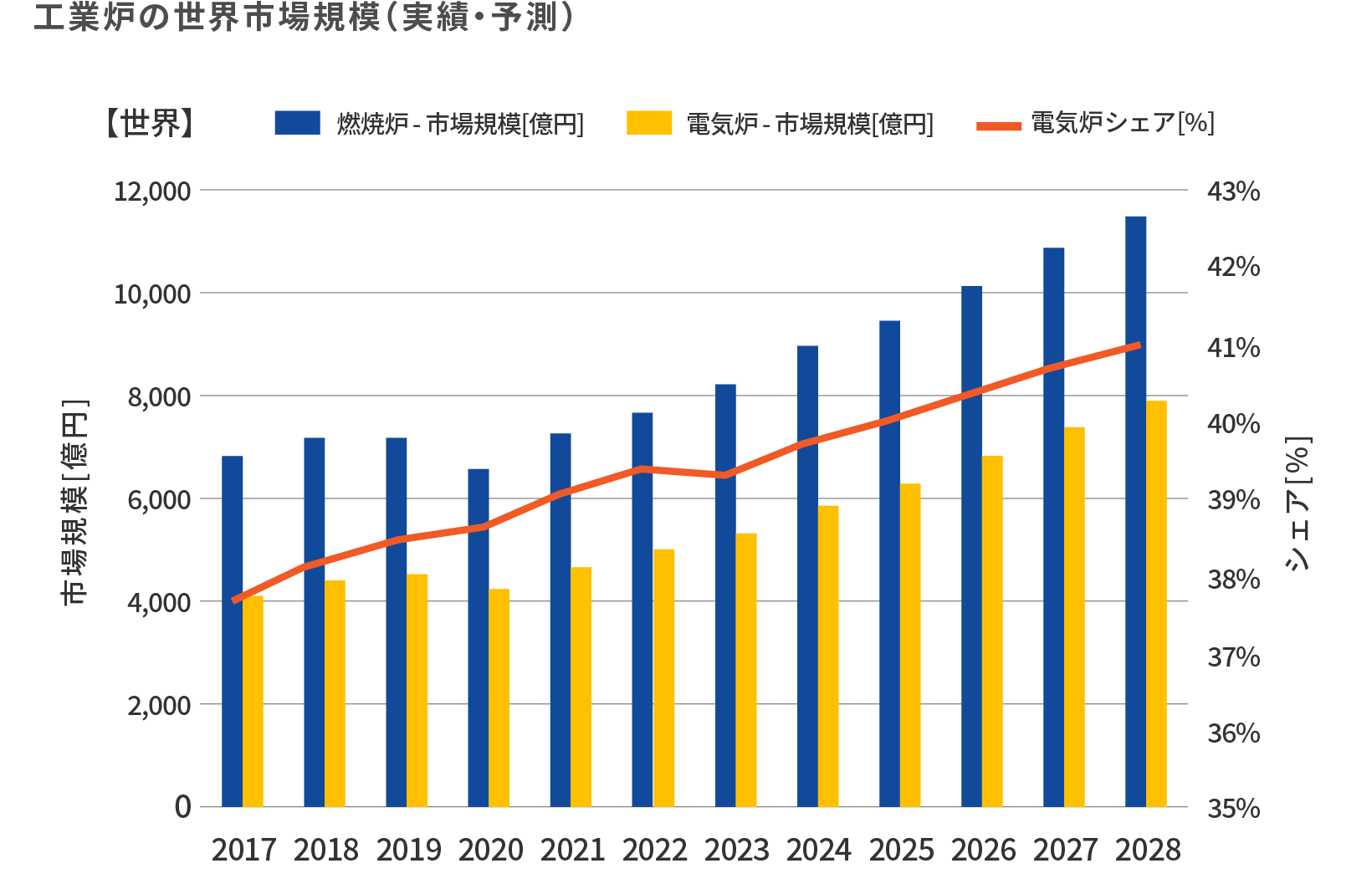
工業炉のカーボンニュートラル化に向けた方向性
工業炉のカーボンニュートラル化には、用いるエネルギーそのもののカーボンニュートラル化に向けた取り組み状況や調達動向等も見定めながら、複数の技術的アプローチを行っていくことが重要です。
燃焼炉においては、従来の化石燃料から、燃焼時にCO2を排出しないアンモニアや水素等のゼロエミッション燃料への転換があげられます。アンモニアや水素はグリーンイノベーション基金事業の一環で燃料としての活用に向けた取り組みが進んでおり、先々のエネルギー源として有望視されていますが、工業炉に適用していくためには、金属製品の品質を落とすことなく、安定的に燃焼させる技術の確立が必要です。
電気炉は、金属製品を急速かつコンパクトに加熱でき、利用中のCO2が発生しない特性があります。燃焼炉と電気炉には、異なる特性があることから、どちらも技術的選択肢として確立し、目的や用途にあわせてバランスよく普及拡大させていくことが重要です。
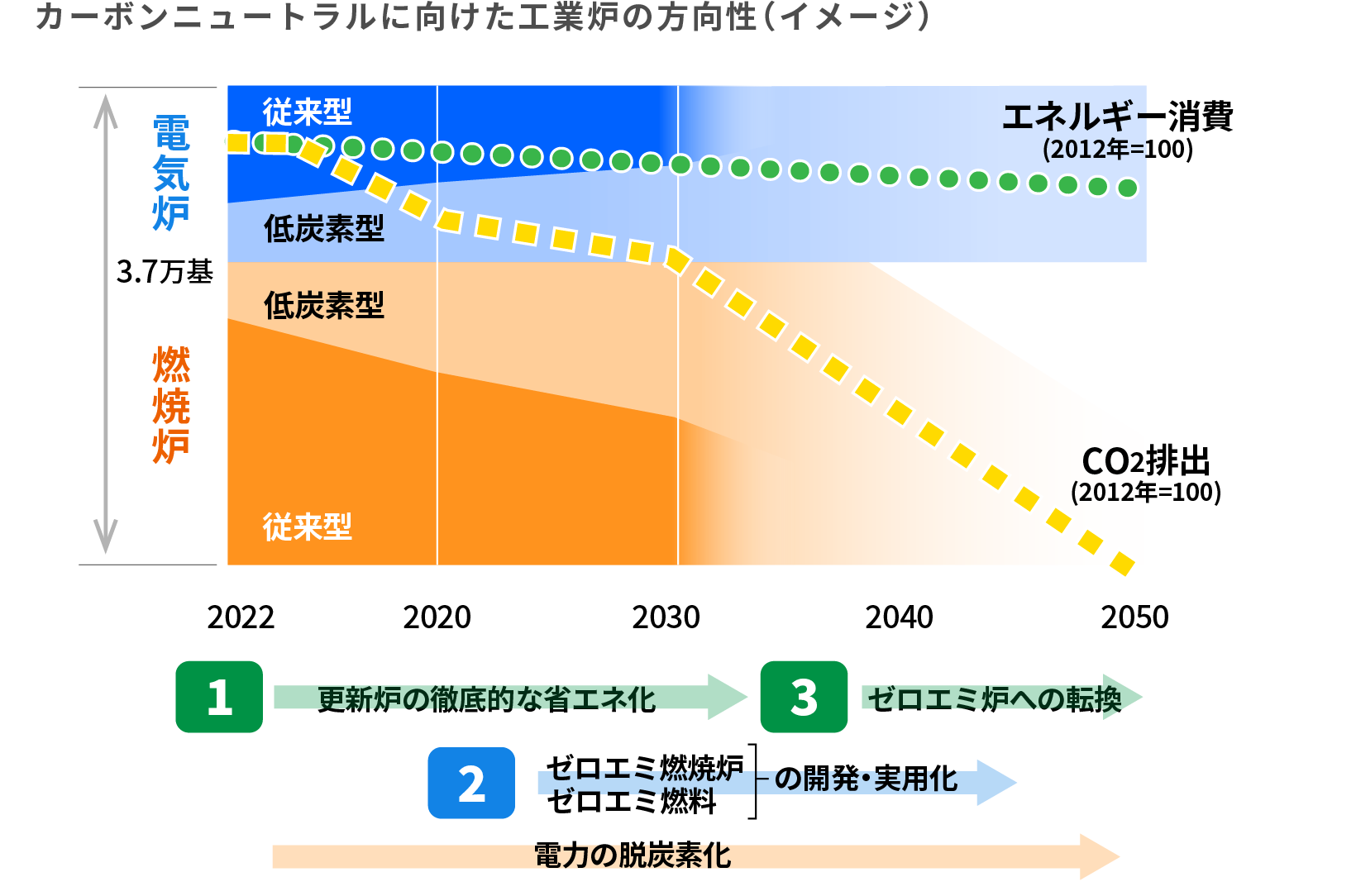
燃焼炉のカーボンニュートラル化、電気炉の普及には、それぞれ課題もあります。
- 燃焼炉にアンモニア・水素燃料を使う場合の主な課題:
- 燃焼速度や火炎温度が従来の燃料とは異なるため、その条件を踏まえた工業炉に改変する必要がある
- アンモニアや水素を燃焼した際に、金属製品等が反応して、硬くなったり(窒化)、脆くなったり(水素脆化)する可能性もあるため、金属製品等への影響の解明と必要な防止策をとる必要がある
- アンモニアや水素を燃焼した際に発生する窒素酸化物(NOx)等を抑制しつつ、安定した燃焼技術を確立する必要がある(NOxは大気汚染の原因の一つにもなっている)
- 電気炉の利用を拡大していくうえでの主な課題:
- 単純に燃焼炉から電気炉に転換する場合、特別高圧電力の契約や受電設備設置が新たに必要となるが、中小企業を中心として、敷地等の制約から対応が困難となることが想定されるため、最も電力を消費する昇温時(ピーク時)の電力消費量を抑えて、受電設備容量を低減する仕組みや、更なる省エネ化が必要である
- 現状、電気炉では技術的に困難な大型炉での均一加熱・均一温度を実現するための制御技術や設計技術を開発する必要がある
製造分野における熱プロセスの脱炭素化に向けて
こうした課題に対してグリーンイノベーション基金事業では、早期に工業炉のカーボンニュートラル化を実現するため、「製造分野における熱プロセスの脱炭素化」プロジェクトに取り組んでいます。このプロジェクトのなかで、アンモニアや水素といった新たな燃料に対応した燃焼炉の実現に向けて、金属製品の品質への影響とそのメカニズムを解明しつつ、窒素酸化物の低下(低NOx化)、燃焼安定性、長期運転を可能とする燃焼技術等の開発や、電気炉の受電設備容量の最小化や高効率化に向けた技術開発、これらの技術の導入に必要となる影響予測、最適設計・運用効率化を可能とするシミュレーション・デジタルツイン技術(インターネット上で現実空間の環境を再現し、検証等をしていく技術)の開発に取り組んでいます。
将来的な電力需給の逼迫リスク、有事等の際におけるサプライチェーンのレジリエンスを高める観点からも、工業炉のエネルギー源の多様化を図っていくことは、我が国製造業の競争力の維持・強化に寄与します。
実用化に向けては、アンモニアや水素のインフラも含めたゼロエミッション燃料の供給体制の整備も関わります。この供給体制については、グリーンイノベーション基金事業で「大規模水素サプライチェーンの構築」や「燃料アンモニアサプライチェーンの構築」プロジェクトが別途動いており、連携を図っていく予定です。
- *1 国立研究開発法人新エネルギー・産業技術総合開発機構(NEDO)グリーンイノベーション基金特設サイト,プロジェクト情報【製造分野における熱プロセスの脱炭素化】関連資料「研究開発・社会実装計画」p3