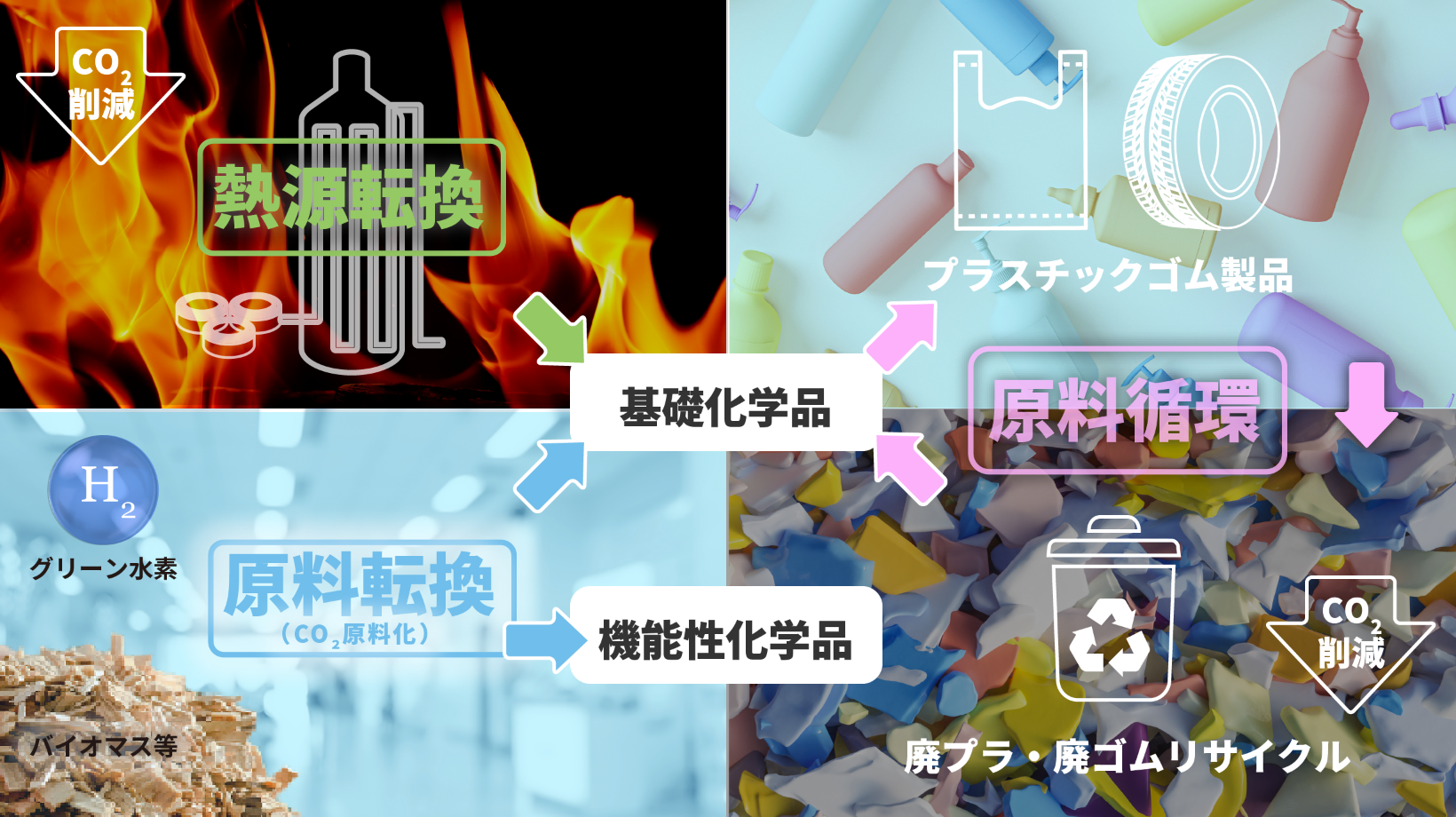
プロジェクト概要
カーボンリサイクルはCO2を資源として有効活用する技術で、カーボンニュートラル社会を実現するためのキーテクノロジーです。日本の部門別CO2排出量の内、産業部門・工業プロセスが占める割合は全体の29.3%(2019年)で、化学産業は産業部門・工業プロセスの内18.6%の年間6018万トンを排出しています。
プラスチック原料のほとんどは石油精製で得られるナフサ(粗製ガソリン)由来であり、化学産業から排出されるCO2の約半分がナフサを分解してエチレン、プロピレン等の基礎化学品を製造する過程等に起因しています。
また、廃プラスチックの約84%がリサイクルされていますが、この内約57%がゴミ焼却発電等の熱源として利用(サーマルリサイクル)され、最終的にはCO2として排出されているため、抜本的な対策が必要です。
そこで本プロジェクトでは、プラスチック原料製造に関する4つのカーボンリサイクル技術(熱源のカーボンフリー化によるナフサ分解炉の高度化技術、廃プラ・廃ゴムからの化学品製造技術、CO2からの機能性化学品製造技術、アルコール類からの化学品製造技術)の開発に取り組みます。
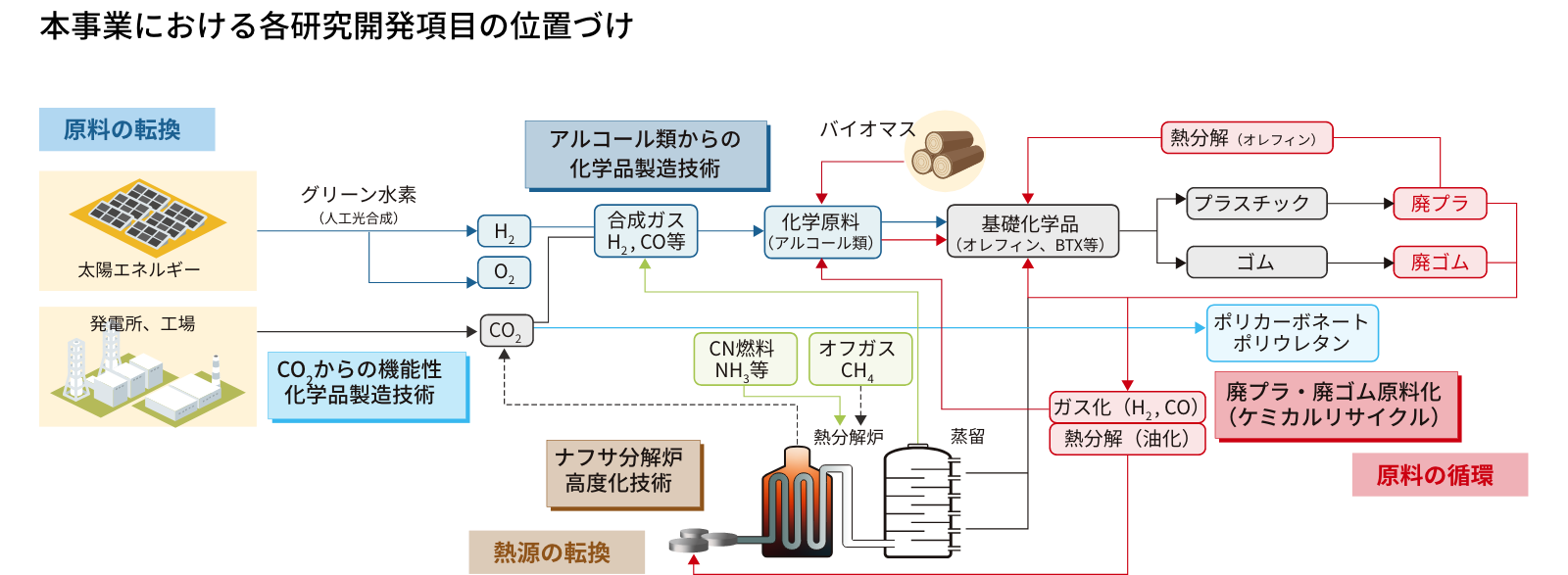
プロジェクトの特徴
〇熱源のカーボンフリー化によるナフサ分解炉の高度化技術の開発
2030年までにCO2を排出しないアンモニアや水素等を熱源としてナフサを熱分解する分解炉およびバーナーを開発し、製造時の消費エネルギー、コストを現行のナフサ分解炉と同程度にする技術の実現を目指します。
〇廃プラ・廃ゴムからの化学品製造技術の開発
廃プラスチックや廃ゴムのガス化や熱分解、バイオマス活用等によって、CO2排出量を大幅に削減し、かつ製造コストを下げる技術開発を行います。数千~数万トン/年スケールの実証で、2030年までに現行ケミカルリサイクルプラスチックと比べて製造コスト2割減を目指します。
〇CO2からの機能性化学品製造技術の開発
CO2からポリカーボネートやポリウレタン等を製造する技術を確立することでCO2排出量を削減し、同時に機能性をさらに向上させる技術を実現します。数百~数千トン/年スケールの実証で、2030年までに既製品と同価格を目指します。
〇アルコール類からの化学品製造技術の開発
高い変換効率(変換効率10%以上)を達成する光触媒を開発すると共に、人工光合成パネルの製造コスト低減、耐久性向上等により水素製造コスト低減(30円/Nm3以下)を目指します。また水素とCO2からアルコール類を経由してエチレン、プロピレン等の基礎化学品を高収率(80~90%)で製造し、製造時のCO2排出量を実質ゼロにする技術の確立を目指します。